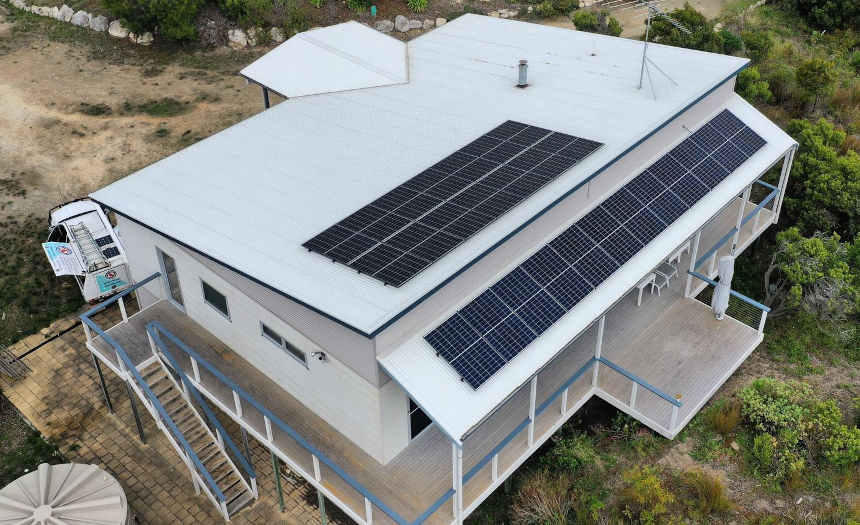
Perfectly simple skillion roof. Image Credit: Josh Sheppard Electrical
As a qualified solar electrician, roof plumber, licensed contractor and supervisor, I have seen the ugly truth behind Australian roofs first-hand. The sad reality is the roofs I’ve worked on could move anyone to tears if only they realised the opportunity missed for both passive and active solar power system design.
Please bear with me. This post is as important as it is long.
Introduction: The State Of Australian Roofs
It’s hard to know what’s driving the way Australians build, but it’s not common sense.
- Fashion seems to dictate insipid monument grey 1 is the only colour to use. If only we could get fleet car buyers to specify houses, there would be more light-coloured roofs, like there are appliance white cars.
- Developer and local government rules dictate you can’t have shiny metal cladding. The grace of aged galvanising is replaced with faded paint.
- Ludicrous complexity has become a virtue.
- We’ve expanded on the subject with more here.
The Issue With Complex Roof Designs
Growing up in a c.1875 house replete with iron lace and solid stone walls, I appreciate that ceiling height is directly proportional to happiness and, more importantly, you can’t have a decent verandah without height to hang it from.
Driving through the suburbs makes me despair. I call it federation virus: turned finials, Dutch gables, bay windows, and “bullnose” verandahs that have almost no curve because the house they’re attached to just isn’t tall enough to legally have both 2050mm headroom underneath and a 5° fall to shed water.
These places look like a poor imitation because they are, but they’re still not as ridiculous as the quintuple-fronted modern house with parapet walled portico.
Just look at it. Call me uncharitable, but whoever designed this roof should be thrown off it. After they’ve been forced to crawl through the ceiling space to run those solar conduits properly.
Builders Aren’t Adventurous, They’re Stuck
There seems to be a perverse power imbalance at play, I’ve often heard people saying:
“The builder won’t let us do that.”
It makes me wonder, who’s working for who exactly?
A couple of two-storey townhouses, where the upper levels have no less than 29 hips, ridges and valleys. The developer lied to the customer that single panels couldn’t work because they didn’t want to buy more expensive microinverters. In any case a terrible roof design.
From the trade perspective, customers looking to change anything, especially ones asking for extra time or material can be seen as troublemakers. Variations are expensive. Just moving a tap could cost hundreds, so savvy investors simply buy what’s on the plans.
If you start talking about energy efficiency, you must be some weirdo greenie, and you’ll cop what is called “the dickhead tax”. For a builder, the easiest way to avoid doing something new, that you reflexively don’t like, is to price it beyond belief.
The sales plan on the right here didn’t pan out. In actual installation on the left was still a bit tricky, but a nice big system on a big house.
Shift To Something Genuinely Good
Just like solar power systems, large sales companies aren’t likely to offer great outcomes. Go with a smaller business, a boutique builder or an architect who’s well-versed in passive solar design. I highly recommend inspecting a display home built to PassivHaus standards. Efficient houses are highly insulated and airtight. They use HRV devices to reclaim energy by pumping fresh air through a heat exchanger, so the air gets changed, but the temperature doesn’t.
Now, Here’s The Kicker.
- To meet passive house standards, a house can only leak 60% of the inside air volume every hour.
- Your average new house in Australia, built to NatHERS 6-star design, will leak 1500%
PassivHaus shows what’s possible, but is probably overkill in Australia, it’s the total opposite of an evaporative air conditioning design, where the air volume is turned over every few minutes. However, many Australians have ducted RCAC air conditioning/heating on what is sadly a glorified shed. You have to spend a lot of money pouring energy in to make them comfortable while the house leaks like a sieve.
It’s Time to Turn the Tables: Lobbying and Profitability in the Building Industry
Energy-conscious builders exist, but they’re outliers. Be under no illusion most of the building industry works for you in the same way that Big Tobacco works for their customers; that is, they put their short-term profits above your long-term interests, by actively lobbying to delay increased energy standards.
Read for yourself, but there’s only one passage I can find anywhere from Master Builders Australia that puts sustainability before profitability. They argue against improved standards, instead saying that software and education will improve things, slowly. If they can get subsidised training.
“Through our advocacy work we’re focused on ensuring your (building) business isn’t overburdened by unnecessary red tape”
“The MBA is lobbying for changes to star ratings for new homes to be delayed until 2025.”
“The Master Builders Association (MBA), representing many large developers and construction companies, said more time was needed and the costs would outweigh the benefits.”
Here we see the benefit of no less than four bathroom vents messing up an otherwise decent roof plane. Image credit: Karl Jensen
So Where Do We Start? Simplicity And Efficiency
The simple answer is: start with simpler roofs. This is an easy win if we explain that it’s cheaper, faster and more efficient to make large rectangular planes instead of complex hips and valleys or problematic parapets and box gutters for a flat roof.
Another skillion, this time on a rendered straw bale house. These off-grid jobs never get old.
If you’re a customer building a new house, demand a split skillion roof with decent eaves and at least a 10° pitch.
If you’re a carpenter or roofer, don’t just accept a square metre rate for any roof, demand a premium for every angled timber or sheet you have to measure and cut.
Rural greenfield site, so there’s no space constraint. There’s SIX frontages, not facing the sun, but facing the road so it looks… impressive?
Twelve solar panels littered all over this lunatic roof design shown below.
And if you’re a building company designing these houses, point out to the punters that every step in the wall and every corner in the floor plan costs time and money. Reduce the hard-to-insulate fiddly building outlines, and most of all, think before you press the “apply roof” button on the computer design. Can there be a little extra eave to make the roof, fascia and gutter straighter and faster?
Here we have four houses under one long single red ridge. We call this a roofers roof. Next door, we have four freestanding houses with no less than NINETY-FIVE individual hips, ridges and valleys… and a solar array that’s admirable for its persistence.
East & West Is The New North: Making The Most Of Your Solar
When Time-Of-Use (ToU) retail plans mean that exported electricity at midday is almost worthless, you can triple the value from your solar panels by generating before 10am and after 3pm. If you have trees or other obstacles, don’t forget that a south-facing roof is still worthwhile. In not-so-sunny Melbourne, a 22.5° pitched south-facing roof will still make 95% in summer and 26% in the pits of winter. Who doesn’t want 26% more?
Some solar installers will have a red hot go if you let them.
Here’s an expensive waterfront example of an elegant solar skillion versus the fashionable folly of a modern pagoda.
Put The Bricks On The Inside: The Importance of Thermal Mass
Thermal mass is important for comfort, so don’t be afraid to put the heavy stuff inside the insulated building where you control the temperature.
This room in Adelaide will stay warm long after the fire goes out and cool long after the summer sun rises, thanks to the lime render and bricks.
The same room from another angle. Bricks inside. This is the way.
You can clad the outside of a timber framed house with timber, cement sheet or polystyrene, using all the same building ingredients; simply making it reverse brick veneer means it’ll use less energy without any other changes.
Reverse brick veneer. Image Credit: YourHome / Crosby Architects
Explain it to your builder as a double brick building, but smarter.
Engage An Auditor
I’ve seen first-hand a roofing contractor desperately searching the BCA rule book for a clause that would get him out of having to totally remove and re-lay the roof. Why? His workers had installed sarking as requested by the owner, but they’d pulled it tight, so it looked neat.
The customer was furious because every single metre of the stuff has installation instructions printed on it. Pictures show it should sag between purlins (to create an insulating air gap) and they simply had no clue that was required.
Anticon/Blanket on the left is good. Note the green foil sarking has the correct saggy installation, and a picture printed on it explaining how.
Bulk Up Bulk Insulation.
Just 5% gaps in insulation coverage will lower the value from R2.5 to R1.5, so it’s critical that the builders understand it gets fitted neatly, not stuffed in holes, thrown aside or simply left packed in the plastic bags! You must get the place assessed before the linings go in to make sure you’re getting what you paid for.
Scrunched in places, gaps in others. This builder argued (wrongly) that it didn’t matter if the insulation wasn’t sitting directly on the ceiling plasterboard.
Insulation “installed” in the roof, not that it’ll do any good when it’s still packed in bags.
The Bottom Line
If you’re paying hundreds of thousands of dollars for a new house, don’t accept the keys for something that’s 7 stars as designed, make sure the contract includes 7-stars as built.
Your auditor must test it to see that the finished product performs properly. As consumers, we must demand more from the building industry.
Join us next week as I explain more about designing a roof for solar power and integrating the installation.
Footnotes
- surely dark roofs in a hot climate are a monument to stupidity ↩
What I have noticed is that nearly ever skillion roof, is facing the wrong way!
Most are facing South, making it impossible to install any solar panels at all. If only they flipped them.
The modern housing with dark coloured roofs and roads are giant heatsinks raising the ambient temperatures substantially with no room for vegetation to mitigate the above.
Here in New South Wales the laws were recently changed to mandate light colour roofs on new housing.
In The Ponds, western Sydney a homeowner told me that he had a covenant from the land developers sales contract, that the building thereon would have a dark grey roof. Now I understand how it is that when you look across The Ponds estate there is a sea of depressing dark grey.
As a roofer I can assure you that it gets bloody hot on those dark coloured roofs.
Hi Jacob,
The sea of dark grey is depressing isn’t it, almost as dismal as the idea people make rules to enforce it. As a roofer you’d know that a stark white roof is pretty extreme when there’s some bright sunshine, the glare makes you think a welding helmet would be better than your standard sunglasses… and that’s a good thing!
I live in the Ponds NSW, I am not the person concerned. My roof is dark grey concrete roof tiles, wish I had a light coloured roof. Recently I got 4 Whirlybirds vents installed to try and reduce the temp in the roof space. Given the summer that is likely coming after seeing the heatwaves and fires in the Northern hemisphere.
few comments:
-I am currently trying to design a small Passive house. Definitely not easy! There is so much to think about: Where the various membranes are placed, how to source reasonably priced Passivhaus compliant windows & doors etc etc. Even access to forums costs: Passive House assn fees are high, even for a single-building owner builder (this needs to change: otherwise where do we get valuable advice for our reasonable questions?)
– Australian houses leak excessively. Even my own current house built in the ´90s leaks like a sieve. But if houses are sealed, the problem of moisture build up in insulation can be an issue if the membranes are placed in the wrong location ( The insulation should be on the ´hot’ side of the Vapor control membrane)
-Roof cavities need to be properly ventilated in hot climates by something like Vent-a-ridge, but you also need to introduce airflow up the walls between the cladding & the rain barrier membrane.
-Insulation needs to be installed with no air gaps! The pictures above are really not up to spec in my opinion. The air needs to be trapped by the insulation, with no areas that can have a thermal airflow: areas such as around roof truss timbers for instance. Also there needs to be thermal breaks so there can be no conduction along steel building members or long fixings.
– As stated in the article we need rectangular roofs, preferably sited E & W, with most panels on the W. I like the idea of the S3 attachment system to steel roofs, where there is no railing. If used on a tray type roof, there is little under the panels to trap leaves. I like to have a 15 degree slope too so the panels largely auto clean.
-On a passivhaus, penetrations of the air control layer(s) need to be minimised & very carefully sealed. Tradesmen need to be trained to understand the principles. Even cables in conduit need to be sealed. The Blower door test even finds leaks like air through the keylocks!
I feel Passivhaus is where we should be going.
Great summary Doug
For reasonably priced advice the other option is “My Efficient Electric Home”
https://www.facebook.com/groups/MyEfficientElectricHome
Great article Anthony. We need to remember the bigger picture. It is is not just about reducing energy bills. It is also about reducing greenhouse emissions and global warming. Simple roof design and light coloured roofs – not dark grey – do just that.
Interesting read, thanks.
I’m in the early stages of trying to build a steel framed shed from scratch that, due to the slope, will have a raised Hebel floor
https://hebel.com.au/product/powerfloor/ and no thermal mass to speak of. The idea is that if it’s well enough insulated, heating it up should be cheap and quick. For cooling (Clare Valley, SA), opening windows for cross drafts should be enough. Hopefully!
So, the figures we were given as a guide for new builds, grid attached, was for 10 kW of PV panels. If the standard new house is that poorly constructed, how much less do we need to put on the roof in comparison if there’s no thermal bridges and everything is well sealed and insulated?
I know this is a length of string question but if you say a 6 star build needs X kW to heat / cool it, what would the same house but to 9 stars be looking at?
Hi Owen,
I don’t have a good ready reckoner for heating/cooling load however I have a deal of first hand experience with sheds. Firstly I would look at insulating the hebel floor. Good mate of mine cursed the fact he didn’t on a very well finished house beside the river at Morgan. Secondly I would line the entire shed with anticon blanket. Having worked in a shed that was build by a shed builder for his own place, having the whole place lined was remarkably good. Olympic make some pretty good sheds.
Cheers
Thanks Anthony,
The only product I know about for insulating Hebel is closed cell foam sprayed under the slab. If it isn’t illegal, it probably should be due to the gasses it gives off!
The architect who does the Class 1 buildings was suggesting a rubberised thermal break but at R1, not great. I’ll have words about the Anticon blanket.
In regards to a previous article in which you mentioned a solar panel install based on a LandRover “safari” roof design, airgapped from the roof itself, Do you think that mounting the PV panels in portrait allows enough convection air to flow between to help keep both the roof and more importantly, the panels cool and working more efficiently?
Yes Owen, spray foam is pretty wild. Are you using timber or steel joists?
It might be worth looking at a foilboard product? They make under slab insulation now but whether you can get something that would go down as a continuous sheet over the floor joists would be the question I think.
I have built a Hebel house so understand the material. If you have not bought your Hebel yet, also consider Penny Panel or similar. (I used this in a rebuild in Lismore 6 years ago). Penny panel is Fibre cement each side, & Aerated concrete core. It needs to go on a steel joist system.
Also consider Mega-Anchors for the foundation system: Very little or no concrete: A big saving in rural areas.
Have a look at the PassivHaus system, & consider some of their ideas. PassivHaus does not rely on Thermal mass. Could be incorporated in your design with some thought.
regardss, Doug
Clearly energy efficient housing needs to be airtight, and easily controllable openings/fan venting by the resident, but then the most economical purchase of power is easily and cheaply afforded by filling those cheap to build large flat plane roof with PV panels. This is much cheaper, and in most coastal areas of Australia we simply do not need the levels of construction that those whose winters are snow frozen need to adhere to. After air leakage our cheapest energy saving measures are to capture the suns energy before that energy is lost..
Hi,
I built in 1986, slab floors, 20m² Trombe N wall, 30mm foam insulation in double brick walls, 7 water panel heaters from a wetback wood fired range, 75mm roof insulation with 2 vapour barriers, minimal glass on S, W and E walls.
My son is now at lockup stage with a SIP house, slab floor, triple glazing, closed loop exchange ventilation and is off grid.
His is warmer even unoccupied with near zero overnight temperatures.
Design is everything!
Cheers
^^ THIS ^^
Anthony, re “Your average new house in Australia, built to NatHERS 6-star design, will leak 1500%”.
Is that per hour as well? Or maybe a day, a week, a year?
Hi Elardus,
These numbers are a direct comparison. Australians build crap houses.
When passive house standards mean they are concerned about how much air leaks through the slots in your power points, average Australian windows have larger slots made deliberately to leak air & drain condensation if it forms inside the single pane of glass.
Great article, Anthony.
What I did, though, is put the masonry in the middle of of my rural off-grid build, not in an outside wall to leak all the heat before it can do any good. (Unless it’s clad in several layers of thick rockwool batts & a rainproof skin.) A woodheater nook and adjacent niche with HWS over, woodbox under, doubles the masonry mass, as well as capturing HWS heat loss. The raised HWS allows convection recirculation through the in-flue heat exchanger. The back of the masonry is a tiled bathroom wall, warming that with rear leakage.
I first designed the building with a full-length 25m long north skillion at 40 deg for max winter generation, but as the building inspector was checking on the slab, we agreed I’d submit a plan alteration to replace the west gable with another 40 deg hipped roof for an array to grab afternoon sun. So now there’s only 22 m of full N skillion, but still enough for nearly 10 kWp. It helped that it was self-architected, so I just had to spend a couple of hours on the computer to alter four views. (And it was well before ordering roof trusses. An owner-build doesn’t go that fast.)
An older post here has me thinking that the second 10 kWp of array, instead of going on the old house, 9m away, could go on the 14 deg south tilted other roof skillion, with racking bringing it up above horizontal. I just worry about wind catching a 20 m long row of portrait panels with e.g. 30 degrees of daylight under them. The prevailing westerlies would zip past in line with the row, so it’s mostly a rogue blast from the south which could be an issue.
I laid a walkway of 3 slightly spaced 4x2s under the 1.75m high ridge, so it’s possible to walk stooped for 16m in the ceiling space before meeting the firewall separating the two halves. (I forgot to make the width the same as the space between the tin cheeks of a cabling roll, so you could shoot it down the rails at speed.)
Roof: 77% reflective “Whitehaven” colourbond. KlipLok = no holes.
Sounds great Eric,
I would look at the design using pvwatts.nrel.gov/ and see if the angle frames are even worth it. They’ll cost a lot in terms of real estate to get row spacing, you’re likely just better off with south facing panels laid flush… and more of them.
Or this:
https://www.solarquotes.com.au/blog/solar-flat-roof-east-west-tilts/
Many thanks for the reminder, Anthony. PVwatts shows that the 14 deg south tilt can yield 65% of the alternative 7 deg west roof on another building, in the worst months; June & July. And if, as you’ve suggested, I whack in a second row, flat to the roof, there’s ample yield and minimal wind issues. I think you’ve done this before. 😉 (The other roof is old corrugated iron, and would need new penetrations for fixing. The new KlipLok roofs don’t. )
Incidentally, the 600 mm horizontal inverter & battery exclusion zone from a window into a habitable room couldn’t rationally apply to the window of a workshop where I hope to mount the equipment _inside_, I figure. Anyway, we’ll find out as things proceed.
Sneaking up on this is giving time for design optimisation; “Plan twice, build once.”
…& with your Kliplok roofing have a look at the S3 mount system. No rails & more room under the panels.
Thanks, Doug. I’ll take a look.
What I’ve had pencilled in is Sunlock SLRC700 roof clamps. They’ll just manage the 40 degree tilt on the north facing 10 kW array. (I insisted the roofer additionally fix each sheet with a screw in a top corner, to prevent the array sliding the sheets off the clips.) The datasheet illustrations show the racking raised to about twice the rib height by the roof clamps, so perhaps 70 mm above the decking tray. I’d figured that’d be enough for leaves to clear.
The installation specification stipulates that the roof clamps must clamp over the under-sheet clips, so that the sheetmetal is not used as a structural member. I figure that the over-clip clamping will also help hold the sheeting on the clips in a cyclone. As panel clamp zones won’t match roof clip positions, I see rails run parallel to the ribs as the only way to properly place clamps, maintaining structural integrity.
I will admit to thinking that a rail balanced along a sheet rib is as rigid as a wet noodle, but anticipate that a good installer will not need reminding to add diagonal bracing a couple of places, especially in a 23m long array. Whether transverse rails are needed, or panel rims can serve structurally, will become clear at the time. More rails sounds better to me.
Look up the S3 system: The clips screw to the ribs on the sides. The panels sit on top of the clips. No rails, so a big saving. I would think the best way to mount panels on S3 clips would be Landscape. (I am not an installer, but saw this system at a recent conference & was inpressed)
Thanks, Doug. A quick search for “S3 solar panel clips” only brings up “S5” and a lot of chaff.
In any event, the notion of omitting rails still fails entirely to address the problem that clamps are only allowed to be installed over the under-sheet clips holding the roof down. That is to avoid risky reliance on the sheet as a structural member – a role it cannot reliably fill. (Permissible panel clamp positions will _not_ match existing under-sheet roof clip positions. That is a given.)
Not only are sheet ribs not rated as structural members for array support, but fitting the panel clamps over the roof clips makes the roof fixing more secure in high winds, and they are in increasingly ready supply.
Not only does the atmosphere hold 7% more moisture for every additional degC, but the latent heat of condensation of massive amounts of water vapour increasingly fuels cyclones to catastrophic energy levels, with impressively destructive effects. as we continue to increase CO₂ emissions, while earnestly promising that we’ll decrease them someday. There are now three certainties: Death, Taxes, and that the chickens coming home to roost will dwarf Rocs when they darken our skies. Repeatedly. For centuries.
The plan currently being implemented seems to be to make our atmosphere sufficiently Venusian that solar power generation is occluded by eternal overcast. Then we will pay whatever it costs for nuclear power, and old monopolies will rise from the grave. “Vengeance is mine.” said the oligarchs, in one reverberating voice.
Hi Erik,
I think Doug is talking about S5! and their frameless mountings which do indeed use the roof cladding. (I’m a little surprised it hasn’t taken off more in Australia?)
https://www.s-5.com/products/solar-panels-on-metal-roof-pvkit-2-0/
Sadly you might be correct about the state of the atmosphere, we must get on with the democratisation of energy.
Hi Anthony,
Thanks for elucidating that S5! is the product in question. It looked interesting, but no matter how good the clamps are, they cannot rectify insufficient structural strength in the sheet roofing. I seem to remember reading of different grades of steel being obtainable, so higher grades might take the load, with regulation batten spacings. I believe mine is nothing fancy, so doubtless not up to structural duty.
What has stopped me in my tracks is the “feet” pictured for “trapezoidal” roofing, which may or may not fit KlipLok. They merely have four holes for screws to go through the roofing rib!!! They are not a clamp at all, for heavens sake.
I chose Rolldeck here 30+ years ago, for zero penetrations for fixing. On the off-grid build, KlipLok has done the same job. There is absolutely no way that I will even fleetingly consider allowing a couple of hundred holes in my roof for a primitive fixing scheme, no matter how cheap it is. I think I can understand why it has not caught on.
My kitchen and bathroom venting are through-wall and to the soffit respectively, so the woodheater flue is the only roof penetration in 200 sq m.
I’ll have a word to the solar installer about running the array cables up under the ridge capping, so there are no holes for that either. (That’s where there are walkways for rapid transit in the roof cavity, so long as you duck your head going through each of nearly twenty trusses on the longer run.)
It is interesting to compare products, though, as you never know what you’ll find.